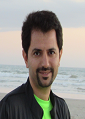
M. Ali Mandegari
University of Stellenbosch
South Africa
Title: Biorefinery annexed to typical South African sugar mill, part 1: flowsheet development and simulation
Biography
Biography: M. Ali Mandegari
Abstract
Sugar is one of the main agricultural industries in South Africa and approximately livelihoods of one million South Africans are indirectly dependent on sugar industry which is economically struggling with some problems and should re-invent in order to ensure a long-term sustainability. Second generation biorefinery is defined as a process to use waste fibrous for the production of biofuel, chemicals animal food, and electricity. Bioethanol is by far the most widely used biofuel for transportation worldwide and many challenges in front of bioethanol production were solved. Biorefinery annexed to the existing sugar mill for production of bioethanol and electricity is proposed to sugar industry and is addressed in this study.
Since flowsheet development is the key element of the bioethanol process, in this work, a biorefinery (bioethanol and electricity production) annexed to a typical South African sugar mill considering 65ton/h dry sugarcane bagasse and tops/trash as feedstock was simulated. Aspen PlusTM V8.6 was applied as simulator and realistic simulation development approach was followed to reflect the practical behaviour of the plant. Latest results of other researches considering pretreatment, hydrolysis, fermentation, enzyme production, bioethanol production and other supplementary units such as evaporation, water treatment, boiler, and steam/electricity generation units were adopted to establish a comprehensive biorefinery simulation.
Steam explosion with SO2 was selected for pretreatment due to minimum inhibitor production and simultaneous saccharification and fermentation (SSF) configuration was adopted for enzymatic hydrolysis and fermentation of cellulose and hydrolyze. Bioethanol purification was simulated by two distillation columns with side stream and fuel grade bioethanol (99.5%) was achieved using molecular sieve in order to minimize the capital and operating costs. Also boiler and steam/power generation were completed using industrial design data. Results indicates 256.6 kg bioethanol per ton of feedstock and 31 MW surplus power were attained from biorefinery while the process consumes 3.5, 3.38, and 0.164 (GJ/ton per ton of feedstock) hot utility, cold utility and electricity respectively. Developed simulation is a threshold of variety analyses and developments for further studies.