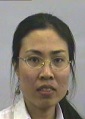
Biography
Biography: Anh phan
Abstract
Biodiesel, a mixture of fatty acid esters formed from a transesterification of triglyceride containing feedstock with a short chain alcohol with or without catalyst, is an alternative to petro-diesel. Biodiesel is superior to petro-diesel because it has low sulfur content, high flash point temperature and lubricity and is biodegradable. It is produced from sustainable feedstock (i.e., vegetable oil, microalgae, waste oil), therefore reducing greenhouse gas (CO2) emissions. Biodiesel production is commonly carried out in batch mode in the presence of alkali catalyst and the required reaction time is up to 2 hours in order to obtain biodiesel that meets a fuel standard (i.e., EN14214). Transesterification is a two-phase reaction therefore the rate of the reaction is mass transfer-controlled. Mixing plays an important role throughout the process due to the low miscibility of oil and methanol initially and byproduct glycerol and esters in the final stages. If the mixing is insufficient, stratification (separation) could occur, therefore reducing reaction rates and this phenomenon is particularly pronounced as the phase separation removes the catalyst from the reaction mixture due to the much better solubility of sodium/potassium hydroxide in the glycerol phase. Oscillatory mixing can be effective method of eliminating mass transfer limitations in two-phase liquid systems due to its mode of mixing. An oscillatory baffled reactor (OBR), a form of continuous plug flow reactor was used to intensify the process. Biodiesel can be produced at an industrially acceptable level (>95%) in 2-5 minutes reaction time, approximately a 60-80% reduction in reactor size to obtain the same throughput. The reactor can be used for multi-stage operations and for two-stage biodiesel production for high free fatty acid feedstock. Another advantage of OBR is that, the scale up is predictable, meaning that conditions obtained in laboratory scales can be used for pilot/industrial scales.