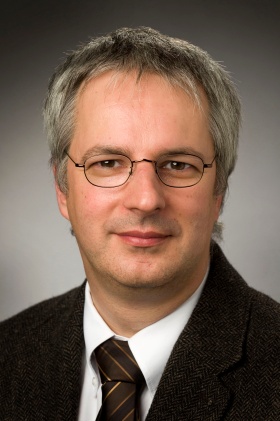
Nicolaus Dahmen
Karlsruhe Institute of Technology (KIT)
Germany
Title: The bioliq-process for synthetic chemicals and fuels production
Biography
Biography: Nicolaus Dahmen
Abstract
The bioliq project aims at the large scale production of synthetic biofuels from biomass (BTL, biomass to liquids). The bioliq process concept has been designed to overcome the problems met, when low grade, residual biomass are to be used to a large extent as required in a BTL process. Biomass such as straw, hay, residual wood etc. usually exhibit low energetic densities, thus limiting collection area and transportation distances. On the other hand, the production of synthetic fuels requires large scale production facilities in accordance with economy of scale considerations. In the bioliq process, biomass is pre-treated in regionally distributed fast pyrolysis plants for energy densification. The products, pyrolysis char and liquid condensates, are mixed to form stable, transportable and pumpable slurries also referred as to biosyncrude. Thus biomass is energetically concentrated allowing for economic transport also over long distances. In industrial plants of reasonable size, the biosyncrude would be gasified in an entrained flow gasifier at a pressure slightly above that of the following fuel synthesis. On site of KIT, a pilot plant was constructed and commissioned for process demonstration, to obtain reliable mass and energy balances, for gaining practical experience, and to allow for reasonable cost estimates. The fast pyrolysis plant has a biomass feed capacity of 500 kg/h (2 MW(th)). A twin-screw reactor, equipped with a pneumatic heat carrier loop with sand as the heat carrier medium is the main technical feature of the plant. The high pressure entrained flow gasifier of 5 MW(th) thermal fuel capacity is an oxygen blown slagging reactor equipped with an internal cooling screen, particularly suited for the conversion of ash rich feeds and fast start up and shut down procedures. The raw synthesis gas is purified and conditioned by a high pressure hot gas cleaning system, consisting of a hot gas filter with ceramic filter elements, a fixed bed adsorption for HCl and H2S removal and a catalytic converter for decomposition of nitrogen and sulfur containing trace compounds. Afterwards, CO2 is separated. The purified synthesis gas is then converted to dimethyl ether in a one-step synthesis process, which in a subsequently following reaction is converted into fully compatible gasoline. Now, the pilot plant construction is completed and first operation took place by commissioning the whole process chain. The process development is embedded into a coherent R&D framework, allowing operation and further development on a science based basis. The pilot plant will be used as a research platform and offers many opportunities for collaborative work and joint projects with additional partners. The bioliq pilot plant is constructed and operated in cooperation with partners from chemical engineering and plant construction industries. Financial support was provided by the Germany Ministry of Agriculture and Food (BMEL), the state Baden-Württemberg and the European Community