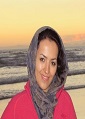
Somayeh Farzad
University of Stellenbosch
South Africa
Title: Biorefinery annexed to South African Sugar mill, part II; energy sufficiency analysis
Biography
Biography: Somayeh Farzad
Abstract
The South African Sugar Industry which has significant impact on the national economy, is currently facing problems due to increasing energy price and low global sugar price. The available bagasse is already combusted in low efficiency boilers of the sugar mills while bagasse is generally recognized as promising feedstock for second generation bioethanol production.
Establishment of biorefinery annexed to the existing sugar mills, as an alternative for re-vitalisation of sugar industry producing biofuel and electricity has been proposed and considered in this study. Since scale is an important issue in feasibility of the technology, this study has taken into account a typical sugar mill with 300 ton/hr sugar cane capacity.
The biorefinery simulation is carried out using Aspen PlusTM V8.6, in which the sugar mill’s power and steam demand has been considered. Hence sugar mills in South Africa can be categorized as highly efficient, efficient and not efficient with steam consumption of 33, 40 and 60 tons of steam per ton of cane and electric power demand of 10 MW, three different scenarios are studied.
The sugar cane bagasse and tops/trash are supplied to the biorefinery process and the wastes/residues (mostly lignin) from the process are burnt in the CHP plant in order to produce steam and electricity for the biorefinery and sugar mill as well. Considering the efficient sugar mill, the CHP plant has generated 5 MW surplus electric power, but the obtained energy is not enough for self-sufficiency of the plant (Biorefinery and Sugar mill) due to lack of 34 MW heat. One of the advantages of second generation biorefinery is its low impact on the environment and carbon footprint, thus the plant should be self-sufficient in energy without using fossil fuels. For this reason, a portion of fresh bagasse should be sent to the CHP plant to meet the energy requirements. An optimisation procedure was carried out to find out the appropriate portion to be burnt in the combustor. As a result, 20% of the bagasse is re-routed to the combustor which leads to 5 tonnes of LP Steam and 8.6 MW electric power surplus.